- Operator intervention is increasingly reduced thanks to improvements in the packaging equipment design.
- Lubrication is one of the main preventative maintenance activities. Respecting the required frequency for this procedure is fundamental as it allows maintenance shutdowns to be planned without affecting scheduled production and it also ensures that your machine operates at peak performance.
What does lubricating the machine involve?
Equipment maintenance is essential to ensuring that the equipment continues to be a useful tool for manufacturers, regardless of the product. All of the machines contain parts which, during operation, rub against each other. In order to reduce this friction and consequently prolong the operational lifespan of the machine’s parts, it is vital to lubricate them on a regular basis. “This procedure, which involves applying—either manually or automatically—a lubricant to a surface, is one of the main preventative maintenance procedures which must be carried out”, explains Oscar Ortega, After Sales Manager at Mespack. “In the case of manual lubrication, a manual pump is used to lubricate the machinery while, for automatic lubrication, we use an electronic pump which pumps the lubricant depending on the needs of the part”.
How frequently is lubrication needed?
The equipment operator has a maintenance manual in which the required lubrication frequency for each part of the machine is specified. “As this frequency varies depending on use”, points out Ortega, “we adjust said frequency according to the working hours recommended by the manufacturer of the part in question”.
What type of lubricant is required?
It is very important that the products used do not pose any risk to the product being packed and, most importantly, to the consumer. To this end, non-toxic, food-grade lubricants with different specifications for different parts of the machine are used “which manufacturers can purchase locally with the same specifications, not being exclusive Mespack products”, explains the company’s After Sales Manager. “This is also stated in the maintenance manual”, he adds
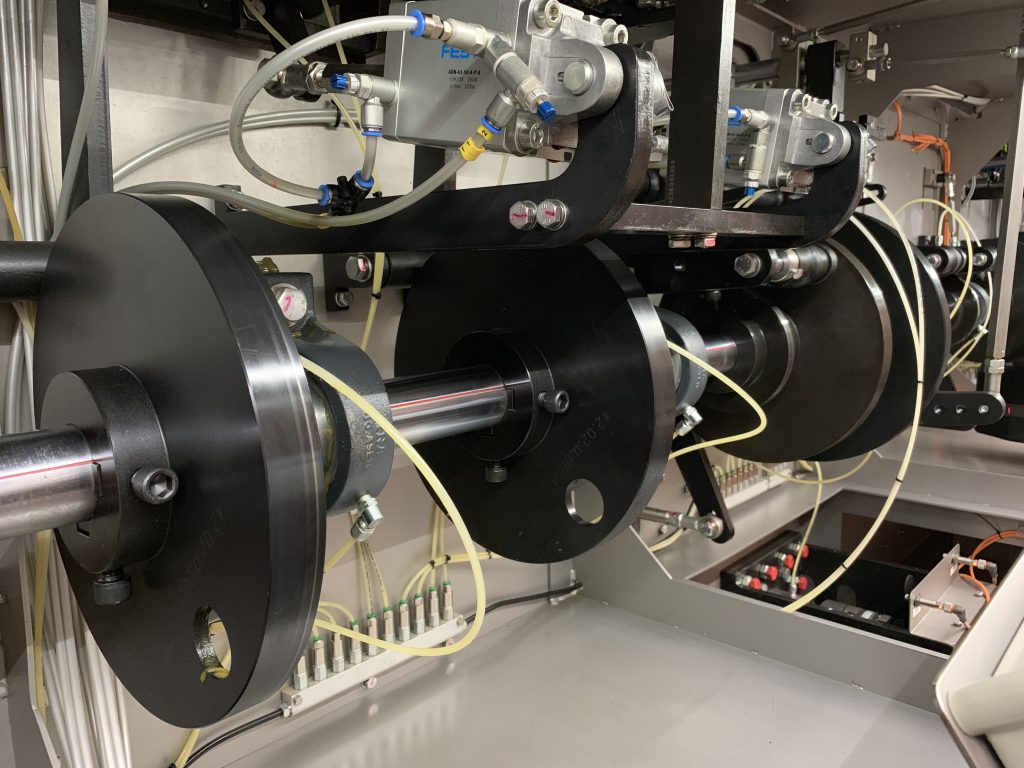
Who can carry out this procedure?
As performing the procedure is not complicated, Ortega states that “people ranging from technical staff to machine operators from each manufacturer can lubricate the machinery. Nevertheless, it is important to note that operator intervention is increasingly reduced thanks to improvements in the packaging equipment design. In fact, the majority of our machines are now delivered with an automatic lubrication system to keep the internal mechanisms of the machine well lubricated.” p align=”justify”>In order to reduce shutdown times even further, customers can also install a complete lubrication system which will lubricate components on the front part of the machine.
What happens if the equipment is not lubricated when needed?
Failure to carry out the lubrication procedure correctly limits the operational lifespan of the machine’s components, giving rise to negative consequences: firstly, in the production process, with the need for unplanned maintenance shutdowns and/or replacement of the affected parts; and, secondly, the potential for other parts of the machine to be affected, causing a much more serious malfunction. Mespack’s After Sales Manager therefore insists that “respecting the required frequency for this procedure is fundamental as it allows maintenance shutdowns to be planned without affecting scheduled production”.