- The Duravant Group company has been working for two years with its key accounts on solutions for enabling its installed base of machines to operate with recyclable packaging and is creating new equipment capable of production with these new recyclable materials.
- Mespack is also collaborating closely with large manufacturers and suppliers of film in order to jointly develop new compostable film.
Today, the flexible packaging industry uses a series of common materials like PET, PP, PE, OPA, aluminium and paper to produce packaging, which all have different properties. PET, or polyester, for example, is highly resistant to wear and corrosion and acts as an excellent barrier against CO2, O2 and humidity. This is very useful for packaging food products. PP, or polypropylene, is also used widely for the rigid packaging of food due to its excellent protective properties and hygiene guarantee. PE, or polythene, is the most widely used material in flexible packaging and is characterised by its versatility, its ability to be sealed and its low cost.
All of these materials, although recyclable separately, require specific conditions to be recycled when they have been mixed to produce packaging materials. In order that the laminate that contains the non-recyclable materials can be recycled, it must be stripped-down, removing the non-recyclable material. Therefore, with the aim of gradually reducing its carbon footprint whilst combating the accumulation of single-use plastic waste, the flexible packaging industry is working together to produce new sustainable material from recycled elements (known as PCR) or organic materials. “PE is often mineral-based, but organic-based PE is now available on the market, which is made from responsibly grown sugar cane, and can be used with fresh, baked, coffee and lactose-based products”, explains Santi Alberich, Mespack’s Marketing Manager. “There’s also 100% compostable packaging, used so that the food waste and packaging compost together, for fresh and baked products”, he adds.
Packaging made from recycled, organic or 100%-compostable material contributes to reducing the flexible packaging industry’s carbon footprint
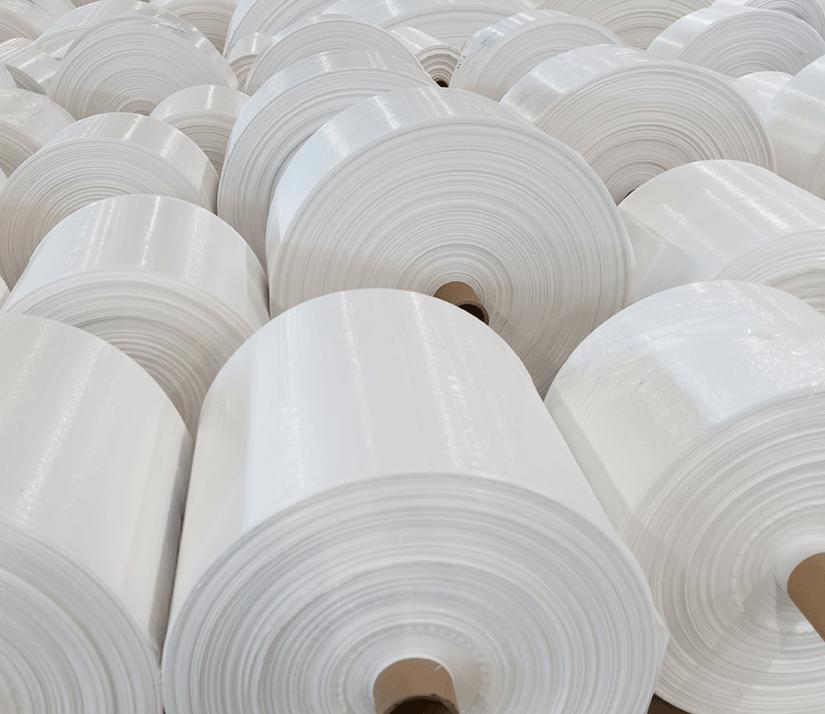
Machines adapted for the future
In order to work with these new recyclable and/or compostable materials, the Duravant Group company has been working for two years with clients like Unilever, P&G and Nestlé, among others, to look for ways to adapt its fleet of installed machines. Moreover, Mespack is working on new equipment designed for optimal functioning with these materials. “For many months we have been carrying out tests with new films, both in our clients’ factories and in our own”, Alberich confirms. “All whilst trying to maintain the same quality and efficiency standards that we have guaranteed up to today with traditional materials”, the company’s Marketing Manager affirms.
As well as this, Mespack is collaborating with film suppliers to create new films and test them in the machines. “We work with recycled film as well as compostable film, which does not currently have a large market presence, but we believe that this is the future”, he concludes.